
How can I access my Beckhoff products remotely?
All this is made possible with the IXON Cloud platform. Using IXON Cloud you can instantly access your Beckhoff PLC, IPC or HMI remotely over a secure VPN tunnel through IXON’s remote service tool. IXON offers a complete and powerful industrial remote access and IoT platform for the Beckhoff product range: IXON Cloud.
What are the supported protocols for Beckhoff PLCs?
Supported protocols for Beckhoff PLCs are: With Cloud Logging, you can configure the data protocol and device address from your IXON Cloud account without any coding. Push the configuration settings to the IXrouter and it will automatically read the data and store it on the IXON Cloud.
Is ixagent compatible with Windows 10 devices from Beckhoff?
This embedded software solution is compatible with Windows 10 devices from Beckhoff, allowing for a wide range of IPCs to be connected to IXON Cloud. Request your IXagent license and firmware via our contact form, and install it on your Beckhoff device to get started.
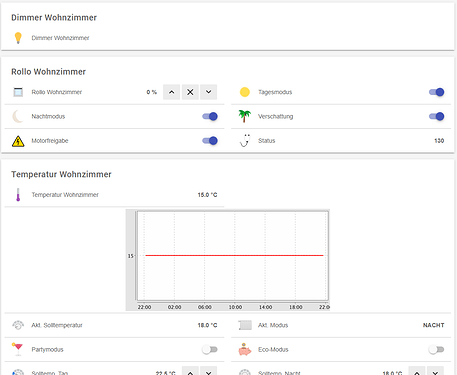
How do I open Beckhoff Device Manager?
Manual start Beckhoff Device ManagerOpen a web browser locally on the Industrial PC.Enter localhost/config in the web browser to start the Beckhoff Device Manager.
What is Cerhost?
With the aid of the Remote Display Control program (CERHOST), a remote connection can be established and an Industrial PC with CE operating system can be remotely controlled from a host PC.
What is TwinCAT beckhoff?
The Beckhoff TwinCAT software system turns almost any compatible PC into a real-time controller with a multi-PLC system, NC axis control, programming environment and operating station.
How do I connect my PC to Beckhoff PLC?
Beckhoff and TwinCATDownload and install Beckhoff TwinCAT 3 programming environment.Once the programming environment is installed, this icon will appear in the system tray.Select > Router > Edit Routes.In the TwinCAT Static Routes window that pops up, select Add...The Add Route Dialog will appear:More items...•
What software does beckhoff use?
The development environment. Beckhoff have chosen Visual Studio (VS) as the development environment for TwinCAT 3 software.
What programming language does beckhoff use?
With TwinCAT 3 Beckhoff uses Microsoft Visual Studio® as the foundation and integrates the configurators and programming languages necessary for auto- mation technology, such as IEC 61131 or Matlab®/Simulink®. The programming languages native to Visual Studio® such as C/C++ or the .
Is Beckhoff software free?
The core of TwinCAT 3 Engineering (PLC programming) is royalty-free and can be installed on any number of development PCs. Various functions/development tools that go beyond pure PLC programming (TExxxx) as well as TwinCAT 3 runtime licenses (TCxxxx / TFxxxx) are chargeable, however.
How do I set up Beckhoff PLC?
StepsBeckhoff Device Manager.Changing NIC Settings.(Optional) Rename PC.Download TwinCAT Runtime, HMI Server, and Google Chrome.Install TwinCAT Runtime, HMI Server, and Google Chrome.Install the Beckhoff Real-Time Ethernet Driver.Run win8settick.bat.Set Firewall Settings.More items...•
How do I upload a program from Beckhoff PLC?
Beckhoff and TwinCATUpload PLC code. Open the TwinCAT XAE in Visual Studio. Select File > Open > Open Project From Target… Select the PLC, then OK. ... Log in to monitor code. Set the target system to the target PLC in the drop down box. Click the green log in button of an arrow pointing into a box.
Who owns EtherCAT?
BeckhoffBeckhoff introduced EtherCAT to the world in 2003. And then in 2004, they donated the rights to the ETG (EtherCAT Technology Group), who are responsible for the promotion of the standard. ETG has a very active developer and user group. EtherCAT is standardized under IEC 61158.
What is a Beckhoff controller?
Beckhoff Automation is a provider of advanced and open automation solutions based upon proven technologies for customers to implement high-performance control systems faster and at a lower overall cost than traditional PLC and motion control systems.
What is PLC programming software?
PLC software allows machines to perform tasks repeatedly to save time, boost efficiency and diminish errors. A programmable logic controller (PLC) is an industrial appliance specifically designed and installed to administer manufacturing processes.
Does beckhoff use Codesys?
CODESYS Control RTE SL is a real-time software PLC for PC-based industrial controllers under Windows - programmable with the IEC 61131-3 development System CODESYS.
What is a PLC in electronics?
PLC stands for Programmable Logic Controller. They are industrial computers used to control different electro-mechanical processes for use in manufacturing, plants, or other automation environments. PLCs vary in size and form factors.
Motion
Our innovative drive technologies give you almost unlimited capabilities when it comes to realizing your application.
Automation
TwinCAT offers many features and various software function blocks for all automation tasks.
MX-System
Our MX-System bundles all technological innovations of automation technology into an IP67-capable construction kit.
How many bus terminals does Beckhoff I/O support?
The Beckhoff I/O system supports around 1000 Bus Terminals and is thus probably the most comprehensive system on the market. The components enable users to operate mixed signal configurations without restriction at each station. This means that a single non-central input/output node can map all of the necessary signals.
What is PC based control?
The PC-based control technology from Beckhoff has proven itself worldwide since 1980 in the widest variety of industries and applications, from the machine controller and the automation of wind turbines to building automation and AV and media technology.
ADS examples
This is great news because it allows you to choose your platform more freely and especially in science many organizations prefer Linux machines in their infrastructure. Here is an example using pyads to read a value from an ADS device:
Remote Access
When developing for our customers using ADS it is often not feasible to have the PLCs and a realistic set of controlled hardware in our own offices. Fortunately it is possible to communicate with the ADS interface of the customers on-site PLC over VPN and SSH-tunneling.
Conclusion
Beckhoff ADS provides a state-of-the-art means of communicating to PLCs over the network. With a bit of configuration this can easily be done remotely in addition to on-site in a platform agnostic way.
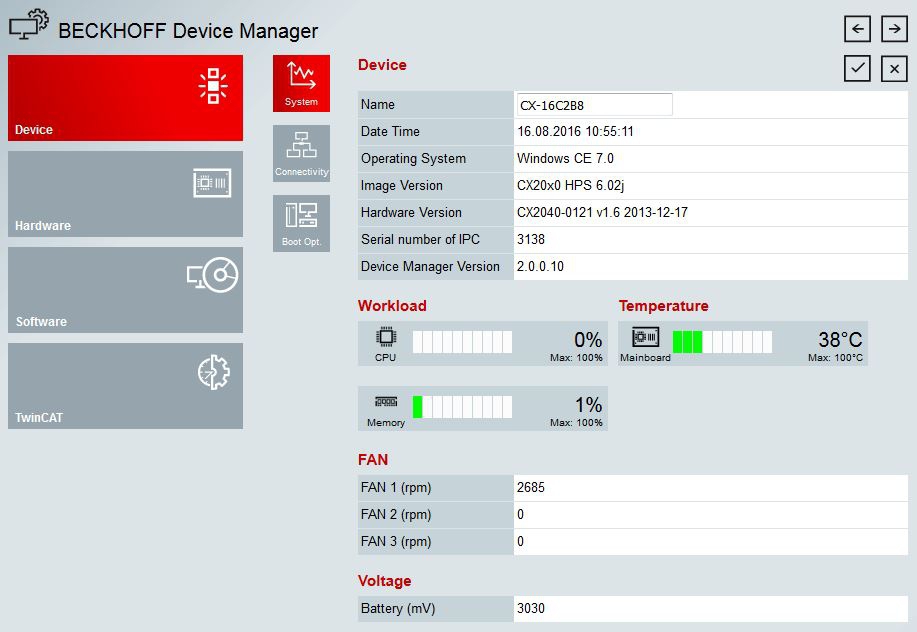